Smart factories : la France à la traîne
La smart factory, l’usine 4.0, totalement interconnectée, devait être la grande (r)évolution des années 2020, transformant en profondeur l’ensemble des moyens de production des différentes chaînes de valeur. On en serait pourtant encore bien loin, en France en tout cas.
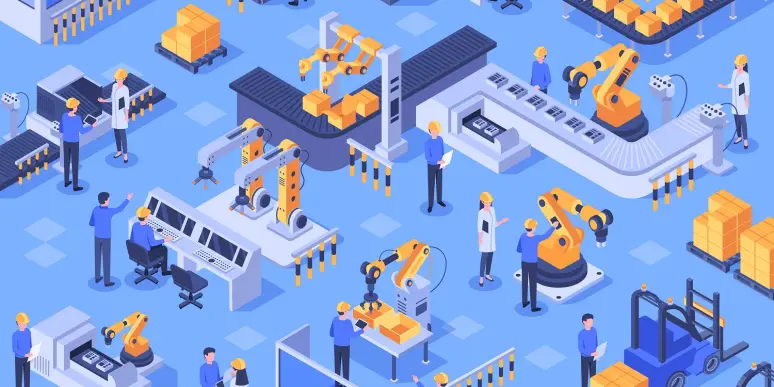
Consultor a interrogé les cabinets qui interviennent régulièrement sur ce sujet, à l’instar d’Oliver Wyman et de Kearney, mais aussi d’une experte du think tank La Fabrique de l’industrie, Caroline Mini.
L’usine 4.0 annoncée comme le messie
Mis en lumière pour la première fois lors de la Foire d’Hanovre de 2011 – l’Allemagne a été un pays précurseur des usines robotisées dès les années 80 –, ce concept d’usine intelligente s’annonçait des plus prometteurs.
La smart factory s’appuie pour l’heure sur une vingtaine de technologies numériques telles que l'Internet industriel des objets (IIoT), l'analyse des mégadonnées, l'intelligence artificielle, la réalité virtuelle et augmentée, la robotique…
Cette production 4.0 promet à la fois d’augmenter la productivité, la qualité, la flexibilité, la customisation, la traçabilité, la sécurité, mais aussi les compétences de ses salariés, et d’entrer dans une vertueuse économie circulaire. La smart factory était ainsi considérée comme la voie royale pour transformer en profondeur le modèle industriel.
En 2017, le rapport dédié, Smart factories at scale, du Capgemini Research Institute, annonçait que la moitié des installations avaient le potentiel pour devenir des usines intelligentes d’ici 2022, avec des gains d’efficacité colossaux à la clé.
« Si l’évolution vers la smart factory prend du temps, c’est parce qu’elle ne concerne pas seulement les technologies mais également les process, les compétences des équipes, les modes de management et les organisations dans leur ensemble. Cela nécessite un profond changement de culture et de fonctionnement de l’entreprise. »
Un état des lieux beaucoup moins 4.0
Ces prédictions des plus prometteuses n’ont pourtant pas l’air d’avoir été concrétisées quelque cinq années plus tard. En tout cas, nous n’en serions qu’aux balbutiements, ou presque. C’est ce que pensent les cabinets de conseil en stratégie consultés qui œuvrent sur le sujet.
« En termes de maturité, sa mise en place se fait à différentes vitesses, avec quelques modèles qui se développent rapidement comme par exemple la Gigafactory de Tesla à Berlin [inaugurée en octobre dernier, le premier site de production de Tesla en Europe vise les 10 000 voitures par semaine – ndlr]. En revanche, les entreprises françaises qui investissent dans ce domaine ne sont pas particulièrement en avance », témoigne Xavier Mesnard, associé chez Kearney au sein de la practice opérations, une spécialité historique du cabinet.
Pour Benoît Gougeon, également associé chez Kearney, il est aujourd’hui difficile de dire quelle est la part de smart factory dans notre industrie. En cause, selon le patron de la practice opérations au bureau de Paris, la difficulté à en donner une définition théorique stricte et à s’accorder sur ses traductions en pratiques : « Il existe une différence de taille entre injecter de l’analyse de données, de la robotique, voire de l’IoT dans un process de production et les utiliser de bout en bout pour synchroniser les flux à travers toutes les étapes des chaînes de valeur. Et en imaginant qu’une définition en vienne à remporter tous les suffrages, les technologies évoluent si rapidement qu’elle serait caduque en moins de cinq ans. »
Un sujet de définition donc, mais aussi d’investissements et de choix industriels nationaux. Dans le domaine, le retard français a été mis en exergue durant la pandémie. La faute à des choix stratégiques de nos industries, selon les experts que Consultor a interrogés.
« Avant la crise, la France était en retard, par rapport à l’Allemagne par exemple, particulièrement en termes de robotisation, qui est l’un des trois piliers des smart factories, avec l’IoT et l’IA/big data. Les différents plans de relance, notamment, ont permis le financement et la mise en place de multiples initiatives de digitalisation dans les entreprises. La crise a eu un effet accélérateur », contextualise Éric Ciampi, partner, responsable de la practice opérations d’Oliver Wyman en France.
à lire aussi

Le Boston Consulting Group a inauguré, mercredi 28 septembre, son Innovation Center for Operations (ICO) à Saclay (Essonne). Il s’agit d’un exemple grandeur nature de ce que peut-être « l’usine 4.0 », matérialisée par deux lignes de production ultra modernes.
Des sites-modèles déjà en marche
C’est la raison pour laquelle même si la smart factory n’est pas encore déployée à grande échelle, quelques sites d'entreprises en France servent aujourd’hui de vitrine à cet idéal d’usine 100 % connectée.
Des expérimentations qui n’ont pas encore été déployées à l’échelle d’un groupe. C’est ce qu’a montré un travail de recensement effectué par La Fabrique de l'industrie. « Le fabricant de textiles ardéchois Chamatex a mis en route une nouvelle usine pour la production 4.0 de baskets sportives haut de gamme. Et cela a permis de rapatrier une partie de la production en France. Somfy utilise l’IoT sur un site à Annecy dans le cadre de sa modernisation. Cela s’accélère car il y a un soutien massif pour l’investissement à l’innovation orienté sur le numérique », assure Caroline Mini, cheffe de projet à La Fabrique de l'industrie, think tank français (dont les deux co-présidents sont Louis Gallois, président du conseil de surveillance de PSA Peugeot-Citroën, et Pierre-André de Chalendar, président de Saint-Gobain).
Des atouts de poids
L’usine 4.0 est-elle pour autant un graal pour le secteur industriel ? Aux yeux des experts, pas sûr. La smart factory n'apparaît en tout cas pas comme la 4ème Révolution industrielle tant annoncée.
« Nous nous situons dans une évolution incrémentale et pas dans des innovations de rupture. En 2007, déjà, Oliver Wyman accompagnait la transformation industrielle d’un fabricant de verres ophtalmiques qui incluait une bonne partie de ces technologies. De même, des robots intelligents sont utilisés dans l’industrie nucléaire depuis une vingtaine d’années. Ce qui a changé c’est que ces technologies sont devenues plus matures et plus accessibles car les prix ont été divisés par dix », rappelle Éric Ciampi.
Même son de cloche pour Caroline Mini : « Nous sommes plutôt dans une phase de transformation numérique des usines, une évolution du modèle d’usine plus connectée qui s’appuie sur les données afin d’optimiser la production, et les matières premières, ce qui permet de diminuer le gaspillage, et de la rendre plus flexible. Avec comme objectif premier la compétitivité et des gains économiques à court terme. C’est une démarche trop récente pour avoir une réelle vision à long terme. Car les gros investissements dans les robots et les exosquelettes sont très nouveaux. »
Gains de productivité, oui, mais pas seulement selon le partner de Kearney, Xavier Mesnard. « Il y a d’autres gains tout aussi essentiels que la réduction des coûts, comme une gestion des stocks plus réactive, un renforcement de la résilience des process, un meilleur pilotage des enjeux RSE ou encore la montée en compétence de nombreuses fonctions… »
Passer à la vitesse supérieure
L’ambition de l’industrie française est donc à présent de concrétiser les potentialités de la smart factory à plus grande échelle. « Il est nécessaire de travailler à s’en rapprocher, même si l’usine totalement automatisée et digitalisée n’est pas la cible à atteindre pour toutes les industries et toutes les géographies », note le partner d’Oliver Wyman, Éric Ciampi.
« Si l’évolution vers la smart factory prend du temps, c’est parce qu’elle ne concerne pas seulement les technologies mais également les process, les compétences des équipes, les modes de management et les organisations dans leur ensemble. Cela nécessite un profond changement de culture et de fonctionnement de l’entreprise », analyse Benoît Gougeon.
Des vraies primes existent pour ceux qui avancent sur cette piste. Éric Ciampi prend pour exemple l’un de ses clients, un équipementier de défense français qui développe une usine en Inde.
« Pouvoir mettre en place ces technologies de bout en bout de la chaîne de valeur (R&D, production, support et services), y compris de la e-réalité virtuelle et augmentée, c’est à la fois travailler plus vite, mais aussi générer beaucoup plus de synergies entre les différents métiers de l’entreprise. »
D’autres devraient alors suivre. Du moins, c'est ce que disent les associés des pôles opérations des cabinets de conseil qui assurent que 100 % de leurs projets dédiés à l’industrie embarquent d’ores et déjà une dimension 4.0.
Un tuyau intéressant à partager ?
Vous avez une information dont le monde devrait entendre parler ? Une rumeur de fusion en cours ? Nous voulons savoir !
commentaire (0)
Soyez le premier à réagir à cette information
industrie lourde
- 17/12/24
Après la forte croissance des années 2010, la chimie française traverse une des phases les plus difficiles de son existence. Les partners que nous avons interrogés s’accordent sur les causes immédiates de la crise, mais les problèmes viennent de plus loin.
- 13/12/24
Au sein du groupe Hilti depuis 2015 et son départ de Bain & Company, Thomas Dropsit, 39 ans, est nommé DG des activités France et Europe de l’Ouest de cette entreprise fondée au Lichenstein en 1941, devenue l’un des leaders mondiaux de l’outillage électroportatif. Il succède ainsi à Guillaume Aberlenc, qui a décidé de quitter ses fonctions après 15 ans à la tête de l’entreprise.
- 08/11/24
Ce sont deux associés du BCG X, Camille Brégé et Paul Ghorra, qui ont quitté le cabinet et le conseil en stratégie pour entrer dans le capital de la PME bretonne Roiné, un constructeur de charpentes en bois. Quasi centenaire, basée près de Vitré (35), une trentaine de salariés, cette société fabrique aujourd’hui quelque 200 bâtiments agricoles et équestres en charpente bois par an.
- 31/07/24
Après quelque 22 ans chez Oliver Wyman, le partner a été nommé directeur des achats indirects (hors métaux et hors énergie) du groupe industriel Constellium, spécialisé dans la fabrication de produits en aluminium. Et ce, dans « le cadre d’un large projet de transformation achats », comme l’annonce la direction du groupe.
- 14/03/24
Passage de témoin à la direction générale de Lafarge France : le 27 février dernier, Xavier Guesnu a succédé à François Pétry, après avoir piloté la filiale polonaise du groupe Holcim durant 6 ans.
- 29/01/24
C’est Laurent Guérin, partner M&A Transformation de Strategy& qui l’a annoncé. PwC France et son entité Strategy& ont accompagné le spin-off du groupe Solvay, concrétisé à l’occasion de la cotation le 11 décembre dernier aux bourses d’Euronext (Bruxelles et Paris) des deux nouveaux groupes (Solvay et Syensqo).
- 22/01/24
Comme en 2023, le bureau parisien de L.E.K. Consulting, promeut un associé en ce début d’année. Il s’agit de Benjamin Tuchman, 35 ans, un consultant maison qui vient d’être nommé partner au sein de la practice Industrials.
- 09/01/24
En « pause professionnelle » depuis septembre dernier comme il l’annonçait lui-même sur LinkedIn, l’ex-consultant de McKinsey Jorge Boucas est nommé président du directoire du groupe Roullier, géant mondial des engrais. De mai à septembre dernier, Jorge Boucas était DG du groupe coopératif sucrier Tereos.
- 07/12/23
Métallurgie, sidérurgie, cimenterie, verrerie, chimie, papeterie… l’industrie lourde représente 75 % des émissions de CO2 de l’ensemble du secteur industriel. Son défi : répondre à la Stratégie nationale Bas Carbone (SNBC) imposant une réduction de 35 % des émissions de gaz à effet de serre en 2030. Simon-Kucher et Kéa accompagnent notamment ces acteurs dans cette lourde transition vers des process plus durables. Et ce, dans une conjoncture complexe pour le secteur.